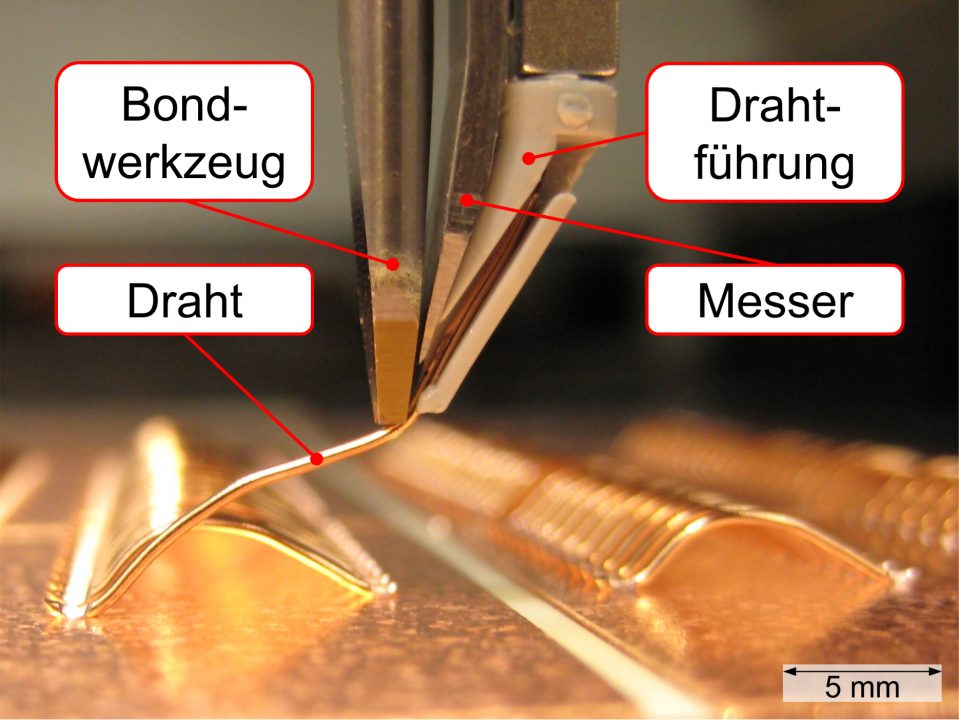
ML4Pro²: Maschinelles Lernen für optimales Ultraschalldrahtbonden
Im Rahmen des it‘s-OWL-Projekts ‚Maschinelles Lernen für die Produktion und deren Produkte‘ (ML4Pro²) arbeiten Fraunhofer IEM als Forschungspartner und Hesse Mechatronics als Industriepartner an intelligenten Verfahren zur Prozessoptimierung und Qualitätsvorhersage für das Ultraschalldrahtbonden auf der Grundlage von Maschinendaten.
Ultraschalldrahtbonden ist ein Standardverfahren für die Herstellung von elektrischen Verbindungen in der Mikro- und Leistungselektronik. Eine Anwendung ist die Herstellung von Batteriemodulen für Elektrofahrzeuge. Die Hesse GmbH entwickelt und fertigt in Paderborn Drahtbondautomaten und vertreibt sie in alle Welt.
Kern des Verfahrens ist ein Kaltschweißprozess, bei dem ein Draht mit einem Substrat durch Zusammenpressen und das Aufbringen von mechanischen Schwingungen im Ultraschallbereich verbunden wird. Das Substrat kann dabei beispielsweise eine Leiterplatte, ein elektronisches Bauteil oder eine Batteriezelle sein. Zwischen zwei oder mehrerer solcher Schweißstellen wird eine Drahtverbindung gezogen und so eine dauerhafte elektrische Verbindung hergestellt.

Die Prinzipskizze (1) zeigt die Hauptkomponenten des Ultraschalldrahtbondprozesses. Das Bondwerkzeug drückt den Draht mit einer Normalkraft FN(t) (t = Zeit) auf das Substrat. Die oszillierende Relativbewegung zwischen Draht und Substrat wird durch eine Wechselspannung US(t) angeregt, der Frequenzbereich ist üblicherweise zwischen 40 und 150 kHz. Die Ultraschallspannung liegt an einem piezoelektrischen Wandler an, der die elektrische Schwingung in eine mechanische umwandelt und über das Bondwerkzeug in die Fügezone überträgt. Die beiden Partner, zum Beispiel Aluminiumdraht auf einer vergoldeten Leiterplatte, werden ohne signifikante Erwärmung durch Metall-Metall-Interdiffusion verbunden. Dieser Vorgang dauert je nach Drahtdurchmesser typischerweise 10-100 ms.
Prozessoptimierung
Die Qualität einer Bondverbindung kann anhand mehrerer Kriterien bestimmt werden. Nach dem Deutschen Verband für Schweißen (DVS) sind insbesondere eine hohe Scherfestigkeit und das Nicht-Vorhandensein einer Kollision von Werkzeug und Substrat wichtig. Die Scherfestigkeit einer Verbindung wird nach dem Prozess mit einer Kraftmessdose in Kombination mit einem Schermeißel gemessen. Der Meißel bewegt sich in geringer Höhe über dem Substrat quer zur Drahtrichtung durch den Bond, so dass der Bond langsam abgeschert wird. Die höchste dabei auftretende Scherkraft ist die Scherfestigkeit. Es handelt sich um ein zerstörendes Verfahren, mit dem daher in Industrieprozessen nur Stichproben untersucht werden können. Eine Kollision zwischen Werkzeug und Substrat kann auftreten, wenn die über Spannung und Normalkraft eingebrachte Energie zu groß ist. In diesem Fall verformt sich der Draht so stark, dass die Flanken des Werkzeugs mit dem Substrat kollidieren und damit möglicherweise beide Komponenten schädigen. Dieses Szenario muss vor dem Hintergrund von empfindlichen, rissgefährdeten Substraten, wie beispielsweise Halbleiterchips, unbedingt vermieden werden.
Das nachfolgende Bild (2) zeigt zwei Schweißstellen unter einem Lichtmikroskop. Der linke Bond wurde gut ausgeformt und weist eine hohe visuelle Qualität auf, wohingegen der rechte Bond ober- und unterhalb Flächen aufweist, welche eindeutig auf eine Kollision hinweisen – seine Qualität ist damit als gering einzustufen.

Um bei der Qualitätsbestimmung das Prozess- und Messrauschen zu berücksichtigen, wird im industriellen Umfeld der Prozessfähigkeitsindex (kurz: CpK) genutzt. Dieses statistische Maß hängt für den Bondprozess von Mittelwert und Varianz der gemessenen Scherkraft sowie von einer für den Prozess geeigneten unteren Spezifikationsgrenze (kurz: USG) ab. Für die Bestimmung der statistischen Werte werden mehrere Bondverbindungen mit den gleichen Einstellgrößen (Zeitverläufe von Spannung und Normalkraft) erstellt und ausgewertet.
Steuerungstechnisch betrachtet besteht das Ziel der Prozessoptimierung damit darin, die bestmöglichen zeitlichen Verläufe für Spannung und Normalkraft vorzugeben, so dass die resultierenden Bondverbindungen einen maximalen CpK-Wert ergeben und gewährleistet ist, dass keine Kollisionen/Toolaufsetzer stattfinden. In der Praxis werden geeignete Parameter bislang experimentell ermittelt. Hierzu ist langjährig erworbenes Expertenwissen notwendig. Des Weiteren ist der Zeitbedarf hoch, da die physikalischen Zusammenhänge sehr komplex sind, mehrere Parameter gleichzeitig eingestellt werden müssen und damit die Anzahl von Kombinationsmöglichkeiten sehr groß ist. Es ist daher umso wichtiger eine gute Planung und guten Überblick über die Experimente zu haben, um redundante und irrelevante Experimente zu vermeiden. Vor diesem Hintergrund ist das Risiko groß, dass auch mit hohem Zeiteinsatz nur ein sub-optimaler Parametersatz (Steuerung) als Lösung gefunden wird, welche die Qualitätsanforderungen nicht oder zumindest deutlich schlechter als ein optimaler Parametersatz erfüllt.
Bayessche Optimierung
Im Rahmen des Projekts nutzen wir die sogenannte Bayessche Optimierung, ein iteratives Verfahren aus dem Bereich des bestärkten Lernens (engl.: Reinforcement Learning), um alle Steuerungsparameter effizient, objektiv und automatisiert zu bestimmen.

Abbildung (3) zeigt die grundsätzliche Funktionsweise dieses Ansatzes. Hierbei sind neben den bereits vorgestellten Größen θ die zu bestimmenden Parameter der Steuerung und l eine binäre Variable, die angibt, ob eine Kollision stattgefunden hat. Der Algorithmus der Bayesschen Optimierung wird nach jedem neuen Experiment ausgeführt und gibt eine neue Parametrisierung aus, mit welcher das nächste Experiment durchgeführt wird. Das resultierende Datenpaar (CpK, l) wird nach dem Experiment an die Bayessche Optimierung zurückgeliefert, woraufhin auf Basis aller bisherigen Datenpaare die neue, vielversprechendste Parametrisierung berechnet und das nächste Experiment gestartet wird. Diese Schleife wird im Versuchsaufbau so lange ausgeführt, bis eine vorgegebene Anzahl an Experimenten erreicht ist. In einer späteren industriellen Anwendung sind weitere Abbruchkriterien denkbar, zum Beispiel das Überschreiten eines geforderten Cpk oder das Erreichen einer geforderten Konvergenz.
Prozessfähigkeitsindex

Das Diagramm (4) zeigt die Entwicklung des Prozessfähigkeitsindex im Laufe der Experimente für verschiedene Materialien und untere Spezifikationsgrenzen (USG). Die Kreise repräsentieren die gemessenen Werte in den jeweiligen Experimenten. Ein Punkt im Kreis deutet an, dass es zu einer Kollision kam. Eine Verbesserung findet somit nur statt, wenn ein höherer CpK-Wert ohne Kollision gefunden wird. Wie gewünscht verbessert sich die Qualität des Prozesses kontinuierlich in allen betrachteten Fällen. Am Ende der automatisierten Einrichtung wird die Steuerung für den Bondprozess beibehalten, welche zum höchsten Prozessfähigkeitsindex unter Berücksichtigung der Nebenbedingung geführt hat. Weitere Details sind in [1] beschrieben.
Qualitätsvorhersage
Ein weiterer Anwendungsfall des maschinellen Lernens besteht in der Vorhersage der Scherkraft einer Bondverbindung, ohne diese zerstörend zu messen. Im Gegensatz zur bisher vorgestellten Prozessoptimierung werden hierbei die Steuerungsgrößen nicht beeinflusst, bzw. verändert. Auf der Basis von überwachtem Lernen (engl.: Supervised Learning) werden aus bestehenden Datensätzen die Zusammenhänge zwischen Steuerungs- und Prozessgrößen und resultierenden Scherwerten gelernt. Auf diese Weise ist es möglich, auch für neue, nicht im bestehenden Datensatz vorhandene Steuerungs- und Prozessgrößen Vorhersagen über die Scherkraft zu machen.

Das Bild (5) zeigt den prinzipiellen Aufbau dieses Konzepts. Als lernendes Verfahren ist ein neuronales Netz (genauer: Long-short-term-memory network, kurz: LSTM) eingesetzt. Hierbei sind die mit einem Dach gekennzeichneten Größen die vorherberechneten Qualitätsgrößen (FS: Scherkraft und l: Indikator für eine Kollision). Der Vektor P enthält alle während des Bondens gemessenen Prozessgrößen, darunter z. B. den elektrischen Strom durch den piezoelektrischen Wandler oder die Höhenabnahme des Drahtes beim Schweißen.

In Bild (6) sind die gemessenen Scherwerte den vorherberechneten Werten des neuronalen Netzes gegenübergestellt. Der gesamte zur Verfügung stehende Datensatz beträgt dabei 1050 verschiedene Datenpunkte für das Material Kupfer und umfasst eine breite Spanne von Scherwerten (700 cN bis 5500 cN). Für das Training werden 900 von den 1050 Datenpunkten benutzt und für die Validierung die restlichen 150. Die Vorhersage ist sowohl auf den Trainings-, als auch auf den Validierungsdaten sehr genau. Dies spiegelt auch die Standardabweichung der Abweichung zwischen Messung und Prädiktion wider, die in diesem Fall 200 cN beträgt. Ausgehend von einer angenommenen Normalverteilung ist die Wahrscheinlichkeit, dass die Qualitätsvorhersage mehr als 400 cN von der gemessenen Scherkraft abweicht, damit kleiner als 5%.
Ausblick
In diesem Blogartikel wurde die Anwendung maschineller Lernverfahren für das Ultraschalldrahtbonden vorgestellt. Konkret wurde die optimale Identifikation der Steuerung (Prozessoptimierung) und Vorhersage der Qualität betrachtet. Für die Prozessoptimierung wurde die Bayessche Optimierung, für die prädiktive Qualität ein LSTM-Netz eingesetzt. In beiden Fällen wurden sehr gute Ergebnisse erzielt, die weitere Forschungsinhalte in diese Richtung motivieren. Zum einen ist hier die Kombination der beiden vorgestellten Ansätze zu nennen. Dabei wird die Bayessche Optimierung nicht direkt am realen System durchgeführt, sondern am neuronalen Netz der Qualitätsvorhersage. Auf diese Weise könnte die Effizienz des Verfahrens deutlich gesteigert werden.
Die nachfolgende Abbildung (7) zeigt ein Konzept hierzu: Der einzige Schritt, der einen Benutzereingriff erfordert, ist das Testen der Bonds (gelb hinterlegt). Der Großteil der Optimierungsdurchläufe (dicke Linien) erfolgt ohne diesen Eingriff mit Hilfe des neuronalen Netzes und somit ungenauer, aber erheblich schneller. Gelegentlich werden die so erhaltenen Ergebnisse validiert und mit dem realen System abgeglichen (dünne gestrichelte Linien). Zusätzlich kann mit diesen Validierungsergebnissen das neuronale Netz verbessert werden (gestrichelte orange Linie), sodass weitere Optimierungsdurchläufe genauer sind. Die Anpassung des neuronalen Netzes muss hierbei nicht in Echtzeit erfolgen. Die Abbildung zeigt analog zu Abb. 5 eine Optimierung der mittleren Scherfestigkeit und des Kollisionsindikators mittels eines neuronalen Netzes und Bayesscher Optimierung. Die Optimierung kann ebenso für Cpk oder andere Größen durchgeführt werden.

Zwar haben sich im Rahmen von ML4Pro² Bayessche Optimierung und ein LSTM-Netz als sehr gut geeignet erwiesen, das Verfahren kann jedoch ebenso mit einem anderen Optimierungsverfahren und/oder einem anderen Prozessmodell (datenbasiert, physikalisch oder hybrid) implementiert werden. Ein Verzicht auf die Prozessparameter als Modelleingang neben den Prozessdaten kann dabei möglich sein, erscheint jedoch wenig sinnvoll.
Wir gehen davon aus, dass die im Projekt untersuchten Verfahren nach Projektschluss zu einem hilfreichen praktischen Werkzeug weiterentwickelt werden können, das sowohl eine Zeit- und Arbeitsersparnis für die Entwicklerinnen und -entwickler industrieller Drahtbondprozesse bringt, als auch verbesserte Prozessergebnisse. Auch die Übertragung auf verwandte Fertigungsprozesse wie das Ultraschallschweißen ist vielversprechend.
Zum anderen wurde hier nur die punktuelle Auswertung der Qualität am Ende des Prozesses betrachtet. Denkbar ist allerdings auch eine kontinuierliche Vorhersage bereits während des Verschweißens, das heißt über die gesamte Prozessdauer in Echtzeit durchzuführen. Die Scherkraft würde damit im regelungstechnischen Sinne beobachtet werden. Hierauf aufbauend könnte eine Regelung anstelle einer reinen Steuerung stattfinden, so dass die Eingangsgrößen sich noch während des Verschweißens an die äußeren Störungen und Gegebenheiten anpassen.
An dieser Stelle möchten wir uns noch einmal bei allen Beteiligten bedanken, die die gemeinsame Versuchsdurchführung trotz der erschwerten Bedingungen durch die Covid19-Pandemie ermöglichten.
Weitere Informationen zum Forschungsfeld Industrial Data Analytics finden Sie beim Fraunhofer IEM.
[1] Hesse M., Hunstig M., Timmermann J. and Trächtler A. (2022): Batch Constrained Bayesian Optimization for Ultrasonic Wire Bonding Feed-forward Control Design. Proceedings of the 11th International Conference on Pattern Recognition Applications and Methods – Volume 1: ICPRAM, S. 383-394. DOI: 10.5220/0010806600003122. PDF (Lizenz CC BY-NC-ND 4.0)